Changing the composition of cement, rather than capturing emissions, could be key to reducing the industry’s climate impact.
View Original Article on SustainableViews >
By Florence Jones
Cover picture: Denis Balibouse/Reuters published by SustainableViews
The cement industry accounts for around 8 per cent of global carbon dioxide emissions, roughly four times that of global aviation. But while its carbon impact is huge, until now projects to decarbonise the industry have been slow to take off.
Cement is a hugely popular building material because of its binding properties, combined with gravel, sand and crushed rock to form concrete. Valued for its durability and low cost, concrete is the second-most consumed material in the world, after water. Twice as much concrete is used in construction than all other building materials combined. But while cement makes up a small proportion of concrete, it produces an outsized share of concrete’s carbon emissions.
Cement is produced by heating raw materials, including limestone and clay, to temperatures as high as 1,450C in a cement kiln, generally by burning fossil fuels. This process produces clinker, which is mixed with gypsum to create cement. Clinker makes up around 11 per cent of concrete in mass, but its production accounts for 88 per cent of concrete’s carbon emissions, says the Energy Transitions Commission think-tank.
In addition to burning fossil fuels, which emit carbon, producing clinker involves the decarbonisation of limestone, which also releases CO₂.
Between 2018 and 2022, cement emissions remained “relatively stable”, increasing by 1 per cent between 2021 and 2022, says the International Energy Agency.
But the IEA warns cement demand is set to grow as developing economies use concrete to build new infrastructure, including that needed for the energy transition. Annual concrete demand is projected to grow from of 14bn cubic metres in 2020 to around 20bn cu m in 2050, an increase of 143 per cent, says the Global Cement and Concrete Association.
Three routes to reducing emissions
There are three possible routes to reduce the cement industry’s emissions, which “complement each other”, say Wouter Vink, lead author of a report on decarbonising cement by the Mission Possible Partnership, and Energy Transitions Commission director Ita Kettleborough.
The MPP is an alliance of organisations founded by the Energy Transitions Commission, the Rocky Mountain Institute, the We Mean Business Coalition and the World Economic Forum.
The first route is to prioritise efficiencies, including improving the design of buildings, extending their lifespan, increasing the use of alternative materials, and reusing certain elements of concrete to reduce overall demand, say Vink and Kettleborough.
Second, they recommend using less clinker in the cement given its carbon intensity. Fly ash, a waste product from coal power plants, and blast-furnace slag, a byproduct from iron production, are potential alternatives.
The supply of these products is expected to fall as greener alternatives replace blast furnaces and coal plants, but “large stockpiles” mean they will play a role in the short and medium term, Vink and Kettleborough tell Sustainable Views. These materials reduce the carbon intensity of cement as they do not undergo the same chemical reaction, and often do not need to be heated to such high temperatures.
Slag from new hydrogen-based production methods, such as green steel production, could be another “significant” alternative as these industries grow, add Vink and Kettleborough.
Other possible supplementary cementitious materials are natural pozzolans, deposits found in areas with volcanic rock, and calcined clay, produced by heating kaolinite, a naturally occurring clay mineral, to temperatures of up to 800C — lower than those required for clinker.
“Alternative materials must be part of a healthy decarbonisation strategy,” Chris Anderson, chief executive of Vantem, a company developing modular, energy-efficient homes, tells Sustainable Views. “New materials that have less embodied carbon are available and can displace a large amount of the cement used today.”
In addition to reducing the emissions released during the production process, alternative materials can also lower emissions during a building’s lifetime, adds Anderson. Cement is “not thermally efficient”, and so without “expensive insulation” buildings constructed with cement require high levels of heating, he says.
Cement from waste products and circular materials
Dublin-based Ecocem is using SCMs to manufacture alternatives to conventional cement. It began using slag to produce alternative cement 20 years ago, Ecocem co-founder and managing director Donal O’Riain tells Sustainable Views.
However, the price of slag has increased “fivefold” over the past 20 years, largely as a result of the EU’s Emissions Trading System, which offers limited emissions allowances for cement producers, pushing some producers to see slag cement as an alternative to avoid buying additional allowances, says O’Riain. Analysis by asset management company Gunung Capital in 2022 projected a 11.8 per cent compound annual growth rate between 2020 and 2026 for sales of slag cement.
Because of rising prices, Ecocem is increasingly focused on making cement production more efficient through a variety of SCMs including pozzolans, reducing emissions by as much as 70 per cent.
The resultant material, known as ACT, has been approved as safe for sale in Europe by the European Organisation for Technical Assessment, says O’Riain. His company plans to continue working with national authorities in France, Belgium, the Netherlands, the UK and Ireland to get the norms governing concrete changed by the end of 2025 and Ecocem’s product deemed as safe to use as conventional concrete.
Influencing national norms is “tricky”, says O’Riain, suggesting “existing cement companies have an oversized influence” on norms committees and are “not necessarily very accommodating of changes that don’t favour their interests”.
In the US, start-up Fortera has developed a production process using pure limestone, rather than a combination of limestone, iron oxide, clay materials and quartz as is the case for conventional cement. The limestone is heated to temperatures of 900C to 1,100C, lower than conventional cement, which causes the limestone to decarbonise. However, instead of the waste CO₂ being emitted, it is re-entered into the reaction along with calcium oxide, also known as quicklime, to form a reactive limestone that works as an alternative to cement and creates a “circular” alternative.
Fortera is operating a small-scale commercial plant in California that has reduced the CO₂ emissions of conventional cement by 70 per cent. Fortera chief executive and co-founder Ryan Gilliam tells Sustainable Views that his company is also looking to electrify the heating process using renewables paired with energy storage or green hydrogen, which would enable a 100 per cent reduction in CO₂ emissions compared with conventional cement.
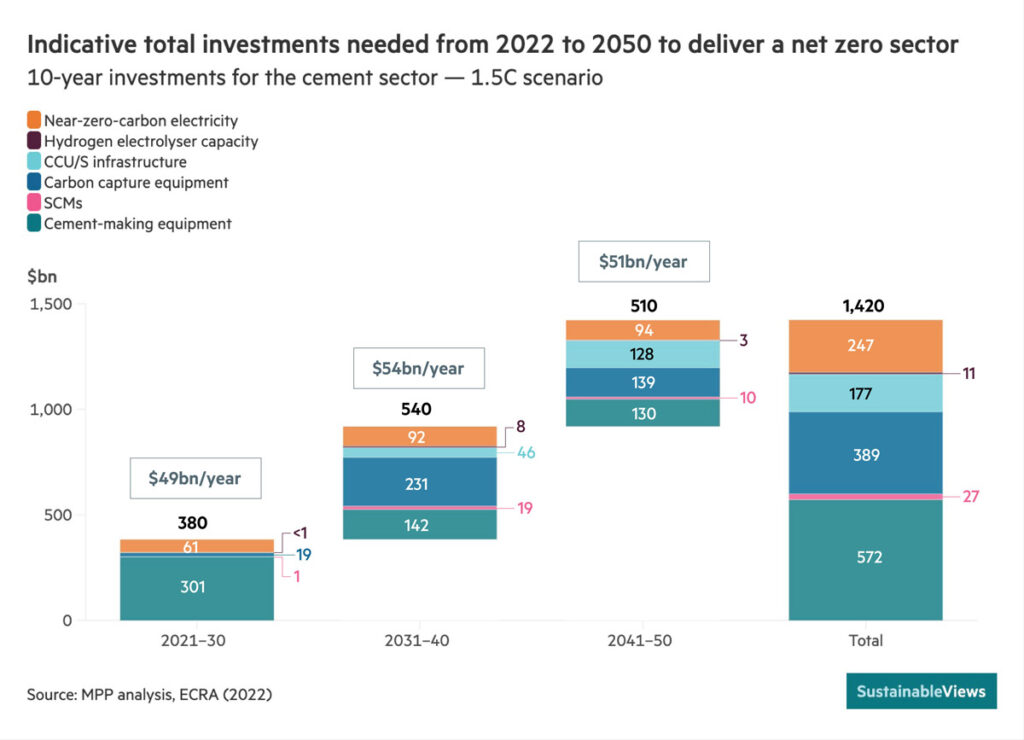
Cement and carbon capture
The third route to cement decarbonisation identified by Vink and Kettleborough, using carbon capture and storage to remove emissions while maintaining a traditional production process, is the one that has received most attention.
“The consensus view by the associations that represent the industry is that the technology of choice is [CCS],” O’Riain says. By favouring CCS, the major industry players can advocate for a business-as-usual approach, he adds. But there are “many problems” with this solution, including that the use of CCS in the cement industry remains at a “developmental stage” and progress is “too slow”, O’Riain argues.
With funding of up to $14.1mn from the Norwegian government, the German cement giant Heidelberg Materials has started constructing a CCS unit at its cement plant in Brevik, in Norway, which is due to be completed by the end of 2024. The plan is for the captured CO₂ to be stored in spent oilfields in the North Sea on the Norwegian continental shelf.
Some small-scale CCS projects have also begun to emerge. Berlin-based start-up NeoCarbon is developing direct air capture technology, which uses waste heat from the cement production process to capture emissions on site. NeoCarbon claims it will be able to transform industrial sites into “carbon sinks” as its technology can capture 1,151,000 tonnes of CO₂ annually at a site emitting 1,084,000 tonnes a year. However, the team is still developing its first minimum viable product and is yet to develop plants at scale.
Other proposed technologies include membrane-based technologies that remove CO₂ emissions at the flue of a cement kiln. UK-based Cool Planet Technologies has developed such a solution, which is powered using electricity, and has signed an agreement with cement manufacturer Holcim Germany to deploy its technology.
But these solutions remain “excruciatingly expensive”, says O’Riain. The MMP report says using concrete efficiently, including designing buildings which use less concrete, using alternative fuels for firing, and reducing amounts of clinker have abatement costs of $35-$20 a tonne of CO₂, while carbon capture costs $160 a tonne.
Simon Gorringe, technical director of Cool Planet Technologies, told a webinar on carbon removal in the cement industry organised by NeoCarbon in June, that the highest cost associated with membrane technologies is not the technology but the cost of transporting and sequestering liquefied CO₂.
In Europe, the necessary pipeline infrastructure “is not fully developed”, he said. Vink and Kettleborough say “infrastructure and investment challenges” will probably be a problem beyond Europe.
CCS has a “complementary role to play in decarbonisation”, but the priority must be using cement more efficiently and using less clinker, say Vink and Kettleborough. “These levers reduce the total volumes of carbon which must be captured, reducing the size of the challenge.”
Originally published on July 9, 2024
To keep informed about latest news follow Vantem on LinkedIn and Instagram